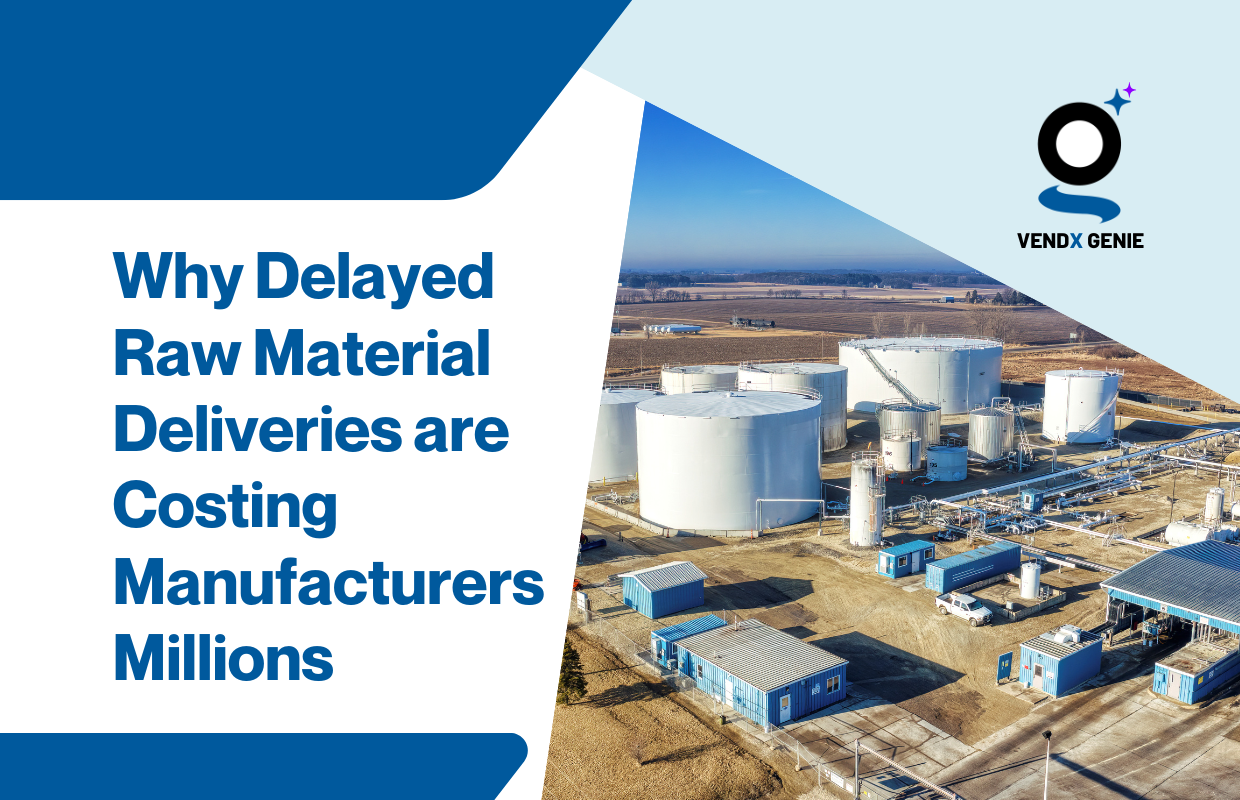
Why Delayed Raw Material Deliveries Are Costing Manufacturers Millions
In the dynamic world of manufacturing, time is everything. A single delay in raw material delivery can trigger a domino effect—halted production lines, increased operational costs, and strained customer relationships. For Indian manufacturers navigating competitive markets and tight schedules, these delays can lead to significant financial and reputational setbacks.
Let’s explore the true cost of these delays, why they occur, and how manufacturers can address them effectively.
The True Cost of Delayed Deliveries
1. Operational Disruptions
When essential raw materials like steel, plastics, or electronic components arrive late, production lines grind to a halt. Every hour of downtime means idle machinery, wasted labor, and backlogs that can take weeks to resolve. For instance, A mid-sized manufacturing unit in India loses over ₹10 lakhs per day during downtime.
2. Missed Revenue Opportunities
Delayed deliveries often result in missed deadlines for finished products, whether automotive parts or consumer goods. This can lead to canceled orders, penalties, or clients switching to competitors. Such losses, especially in industries like FMCG or electronics, can have long-term impacts on revenue streams.
3. Skyrocketing Operational Costs”
Delayed raw material deliveries often lead to skyrocketing operational costs, driven by emergency procurement, expedited shipping, and overtime wages to recover lost time. For example, a day’s delay in receiving raw materials may necessitate air freight or rush orders, inflating expenses by up to 30%. Such unplanned expenditures can erode profitability and disrupt cash flow.
4. Reputational Damage
Consistency and reliability are critical in manufacturing. Chronic delays erode trust with clients, suppliers, and partners, making it difficult to secure future contracts. For Indian manufacturers in export-oriented industries, reputational risks can also impact international partnerships.
Why Delays Happen
- Supplier Reliability Issues
Dependence on single-source suppliers or unreliable vendors increases the risk of disruptions. For example, small-scale suppliers may struggle to meet large orders during peak seasons. When combined with poor communication, these challenges often escalate, leading to cascading delays in the supply chain. - Poor Demand Planning
Inaccurate forecasts can lead to delayed orders or insufficient stock levels, putting unnecessary strain on suppliers. Seasonal fluctuations in industries like textiles or automotive often exacerbate this issue. Poor planning also impacts supplier reliability—when suppliers are overwhelmed with sudden, large orders, their ability to meet deadlines is compromised, creating a vicious cycle of delays. - Supplier and Logistics Challenges
Procurement in India faces risks such as port congestion, transportation delays, and geopolitical tensions. During the pandemic, extended lead times for imported components—such as electronics and raw materials—severely disrupted procurement schedules. These logistical challenges are further amplified by poor demand planning and insufficient supplier coordination. - Inefficient Internal Workflows
Delays in procurement approvals or miscommunication between departments often lead to late orders. Many manufacturers still rely on manual processes, which lack the agility and transparency required in today’s fast-paced environment. Inefficiencies in internal workflows can also make it difficult to respond to unforeseen disruptions, compounding the problem.
Strategies to Prevent Delivery Delays
1. Diversify Your Supplier Base
Relying on multiple suppliers, including local and regional vendors, reduces the risk of disruptions. Nearshoring raw material sourcing within India can also mitigate transportation delays.
2. Leverage Predictive Analytics
Invest in AI-powered tools that analyze historical procurement data and market trends to improve demand forecasting and identify potential delivery risks. Predictive analytics enables procurement teams to anticipate supplier delays and take proactive measures, such as adjusting purchase schedules or sourcing from alternate vendors.
3. Enhance Procurement Process Visibility
Leverage cloud-based procurement platforms that provide live updates on purchase orders, vendor confirmations, and material delivery timelines. These systems enable procurement professionals to monitor order statuses, communicate effectively with suppliers, and address delays before they escalate into larger issues.
4. Strengthen Supplier Relationships
Engage in regular communication with suppliers to ensure alignment on delivery timelines. Establish long-term contracts with performance-based incentives to encourage timely deliveries.
5. Optimize Approval Processes
Streamline internal workflows with digital procurement systems that reduce bottlenecks. For instance, automating purchase order approvals can cut processing times significantly, allowing suppliers to act faster.
The Bottom Line
For Indian manufacturers, delayed raw material deliveries aren’t just operational hiccups—they are critical risks to profitability and reputation. Addressing these challenges requires strategic procurement practices, robust supplier relationships, and investment in technology.
With the right approach, delayed deliveries can shift from being a persistent problem to an opportunity for growth and innovation.
Facing raw material delays? Discover how our tailored e-procurement solution can keep your production lines running smoothly and profitably.
Schedule a free consultation today!
For more such insights follow us on LinkedIn or subscribe to our newsletter. Together, we can build a more resilient and efficient future for manufacturing.